Shift Maintenance Manager
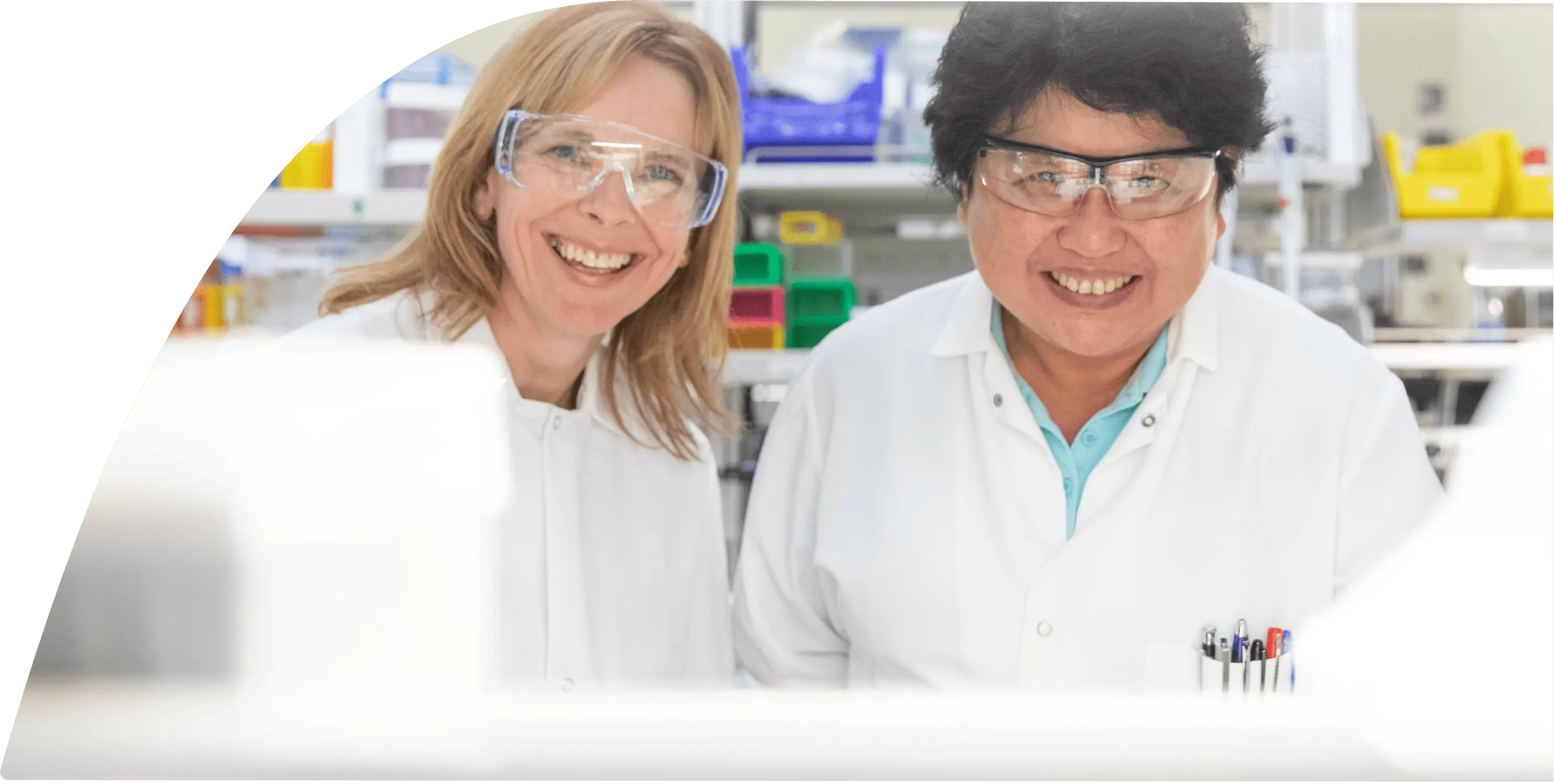
Shift Maintenance Manager
Ireland - Dun Laoghaire Apply NowADL Maintenance Manager (Shift)
Job Summary:
This position will form part of a team of maintenance managers who work together to lead the process maintenance shifts within the Facilities and Engineering function and will report to the Snr. Maintenance Manager on days.
The Shift Maintenance Manager provides leadership and direction to a team of senior maintenance technicians on shift to minimise equipment downtime, provides effective support to equipment breakdowns and manages the execution of the line set-up and maintenance activities safely within the site manufacturing suites.
Key Duties and Responsibilities:
• Providing leadership and direction to the maintenance team supporting the manufacturing processes, maintaining high levels of quality and safety in all operations.
• To manage the execution of the maintenance plan through daily handover, coordination, technical and planning meetings with various plant stakeholders.
• Operates as part of the Engineering/Manufacturing/Quality leadership team visible on the production floor, escalating and communicating effectively using agreed processes consistently to standardise the response to any unplanned events.
• Assigns work to the technician team, actively managing the resources throughout the shift. Engages with and supports the team in meeting standard daily, weekly, and monthly goals.
• Ensures adherence to GxP & SOP requirements for tasks assigned and executed by the team with an ongoing focus on quality.
• Support investigations into process deviations and robust CAPA execution/closure.
• Maintains a high level of supervision and safety compliance during work execution and identifies areas for improvement with the team. Conducts safety walks and provides technical input into incidents and investigations.
• Actively supports the team to manage system access, training and qualification compliance. Maintains team skills matrix and identifies individual skills training needs in conjunction with technicians and the Learning & Performance function.
• Actively supports the team to manage system access, training and qualification compliance.
• Delivers the monthly maintenance plan across the production suites ensuring opportunities to access highly utilised equipment are coordinated and realised.
• Proactive administration of work orders in the CCMS (Maximo), ensuring documentation is accurate and logged contemporaneously with minimal rework or backlog generation.
• Highlights capacity constraints and provides direction on prioritisation at planning meetings to create an integrated and robust manufacturing plan.
• Aligns forecasted maintenance hours and resources with the planning teams. Refine plans at point of execution to balance priorities as part of a cross functional team.
• Coordinates an effective response to emergencies and equipment breakdown by minimising maintenance downtime and executing corrective maintenance efficiently.
• Ensures work completed each shift is documented and handover communication, both written and verbal, is standardised, robust and comprehensive.
• Identifies waste and works to remove plant bottlenecks and flow interrupters.
• Provide technical input for engineering trials and equipment related project activities.
Basic Qualifications:
• Bachelor’s degree in engineering or equivalent qualification and/or experience.
• Minimum of 5 years' experience in a GxP or other highly regulated manufacturing environment with at least 2-3 years in a supervisory role.
• Experience in Lean Transformation and/or Change Management Programs.
Knowledge and Relevant Experience:
• Working knowledge of pharmaceutical/biotech industries and/or aseptic processing.
• Fundamental knowledge of applicable regulatory requirements (GxP & EHS).
• Quality systems management (e.g., Non-Conformance, Change Control, CAPA).
• Equipment troubleshooting and maintenance strategies and systems.
• Resource planning, scheduling and prioritisation.
• Knowledge of relevant computer systems and applications (e.g., Maximo, SAP, Learning Management System, Process Control Systems, Electronic Batch Records).
• Continuous improvement tools and methodologies.
Skills:
• Demonstrated leadership skills with the ability to build teams and operate across functional boundaries.
• Ability to articulate and escalate issues professionally and efficiently.
• Problem solving and logical mindset to navigate complex issues.
• Time and resource management skills at both tactical and strategic levels.
• Strong communication skills (verbal and written) at all levels.
• Team player, prepared to work in and embrace a team-based culture that relies on collaboration and engagement for effective decision-making.