Supply Chain Manager, External Planning & Delivery
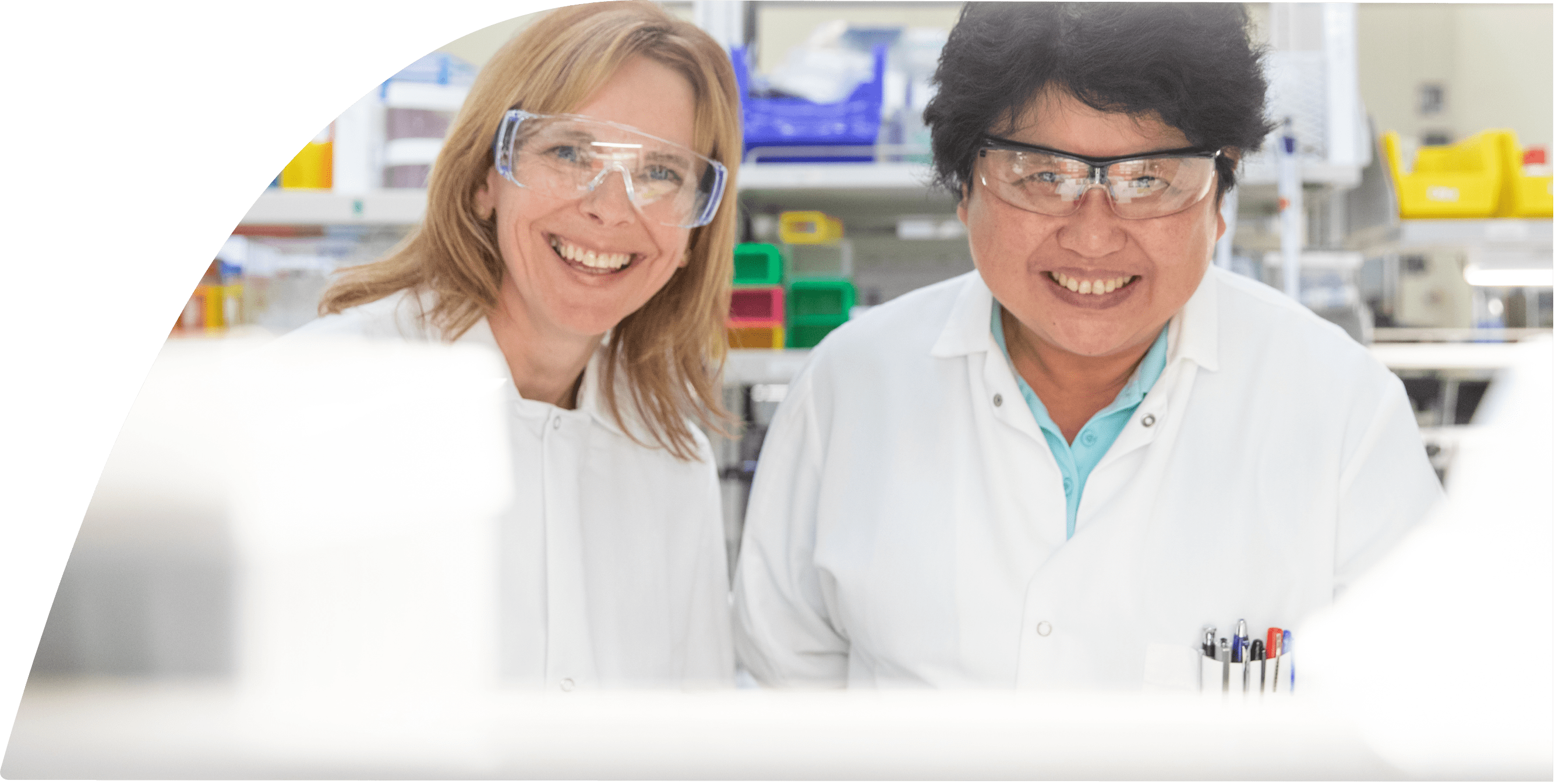
Supply Chain Manager, External Planning & Delivery
Japan - Tokyo Apply NowOverview:
The External Planning & Delivery (EPD) Supply Chain Manager will play a critical role in establishing the
end-to-end supply chain of Amgen’s commercial product portfolio. The EPD Supply Chain Manager will drive
commercial planning and delivery of commercial products manufactured at Amgen’s Contract Manufacturing
Organizations (CMO) in Japan. The overall goal for this position, in tight partnership with Global Supply Chain and Amgen Contract & Development Manufacturing (ACDM), is to deliver supply in the right product quantity to the right location at the right time, while optimizing inventory and cost within the contractual terms, eliminating stock-out and scrap exposure while improving the overall supply risk profile.
Key Responsibilities:
The EPD Supply Chain Manager is responsible for:
- Utilize planning systems (SAP and Rapid Response) to analyze demand and supply requirements.
- Support Amgen’s Integrated Business Processes at the site level, including Plan-to-Stock and Order-to-Cash handoff processes with CMOs.
- Manage purchase orders and invoice processing.
- Develop standard requirements for Technology Transfers and New Product Introductions at CMO sites.
- Ensure implementation and maintenance of required operating standards.
- Collaborate with key stakeholders in supply chain, quality, finance, process development, and operations.
- Deliver reports, presentations, and recommendations to executive audiences.
- Serve as a supply chain resource for special projects and initiatives.
- Operate independently, adhering to Amgen Values and Leadership Attributes..
The EPD Supply Chain Manager will carry out the following activities per established business processes and procedures. These tasks may vary according to the product portfolio:
Production Planning:
- Create and manage master data (design, setup, and change control assessments).
- Translate demand into executable production plans through forecasting.
- Manage xDP planning and allocation (demand bulk, production allocation, weight allocation forms).
- Oversee MRP for DS, DP, and FDP supply and demand.
- Execute production and material transfer orders in SAP.
- Generate and manage process and purchase orders.
- Review and approve invoices.
Raw Material Management:
- Design and set up master data, including change control assessments.
- Determine order policies (quantities, delivery timing, safety stocks).
- Forecast to vendors and internal sites.
- Manage purchase orders and resolve issues with vendors and internal sites.
- Review and approve invoices.
- Plan for storage and space requirements.
Logistic Management:
- Schedule shipments with shipping/receiving sites and vendors.
- Create official shipping lanes for GMP product shipments.
- Lead shipping readiness meetings.
- Provide and review data for import/export documentation for products and samples.
- Generate and manage import/export documentation for raw materials.
- Plan for storage and space requirements, ensure correct storage requirements applied and sufficient storage capacity.
Basic Qualifications:
- Doctorate degree OR
- Master's Degree + 2 years of Supply chain, Business Management, Engineering or Life Science OR
- Bachelor's Degree + 4 years of Supply chain, Business Management, Engineering or Life Science OR
- Associates Degree + 10 years of Supply chain, Business Management, Engineering or Life Science OR
- High School Diploma/GED + 12 years of Supply chain, Business Management, Engineering or Life Science
Preferred Requirements:
- Bachelor’s degree in Business Management, Engineering or Life Science or advanced degree
- Significant supply chain experience in a regulated manufacturing environment
- Proficiency in SAP and Rapid Response ERP systems.
- Strong communication, analytical, and negotiation skills.
- Demonstrated experience in a continuous improvement role utilizing tools, methodologies, and change management (i.e. Lean, Six Sigma)
- Demonstrated strong analytical skills, business acumen and risk management Training and/or demonstrated experience in manufacturing systems
- Demonstrated ability to effectively engage diverse, global stakeholder groups and manage projects with multiple, cross-functional deliverables
Competencies
Knowledge and Technical Expertise
- Understand basics of quality systems, manufacturing processes, and supply chain principles.
- Uses supply chain expertise to identify and resolve conflicts between procedures, requirements, regulations, and policies
- Able to apply principles of finance and accounting Leverages basic Operational Excellence and project management skills
Accountability & Responsibility
- Effectively manages internal and external stakeholder relationships Reprioritizes work during unexpected situations or changing client needs
- Establishes performance metrics to continually improve performance
Communication
- Effective communication across geographies and cultures, with fluency in English and Japanese.
- Understands nuances of a matrixed work environment.
- Conducts presentations and briefings to Sr Management.
- Collaborates with partners by considering input and promoting trust among all parties.
Problem solving and decision making
- Effectively navigates through ambiguity to resolve issues
- Streamline processes using Operational Excellence methodology and tools
- Conducts scenario analyses to evaluate implications of different courses of action
- Maintains composure and direction in high-level situations
- Teamwork and Leadership
- Influences and inspires without authority
- Collaborates and builds constructive cross-functional relationships
- Effectively manages and resolves conflicts