Engineer - Process & Equipment
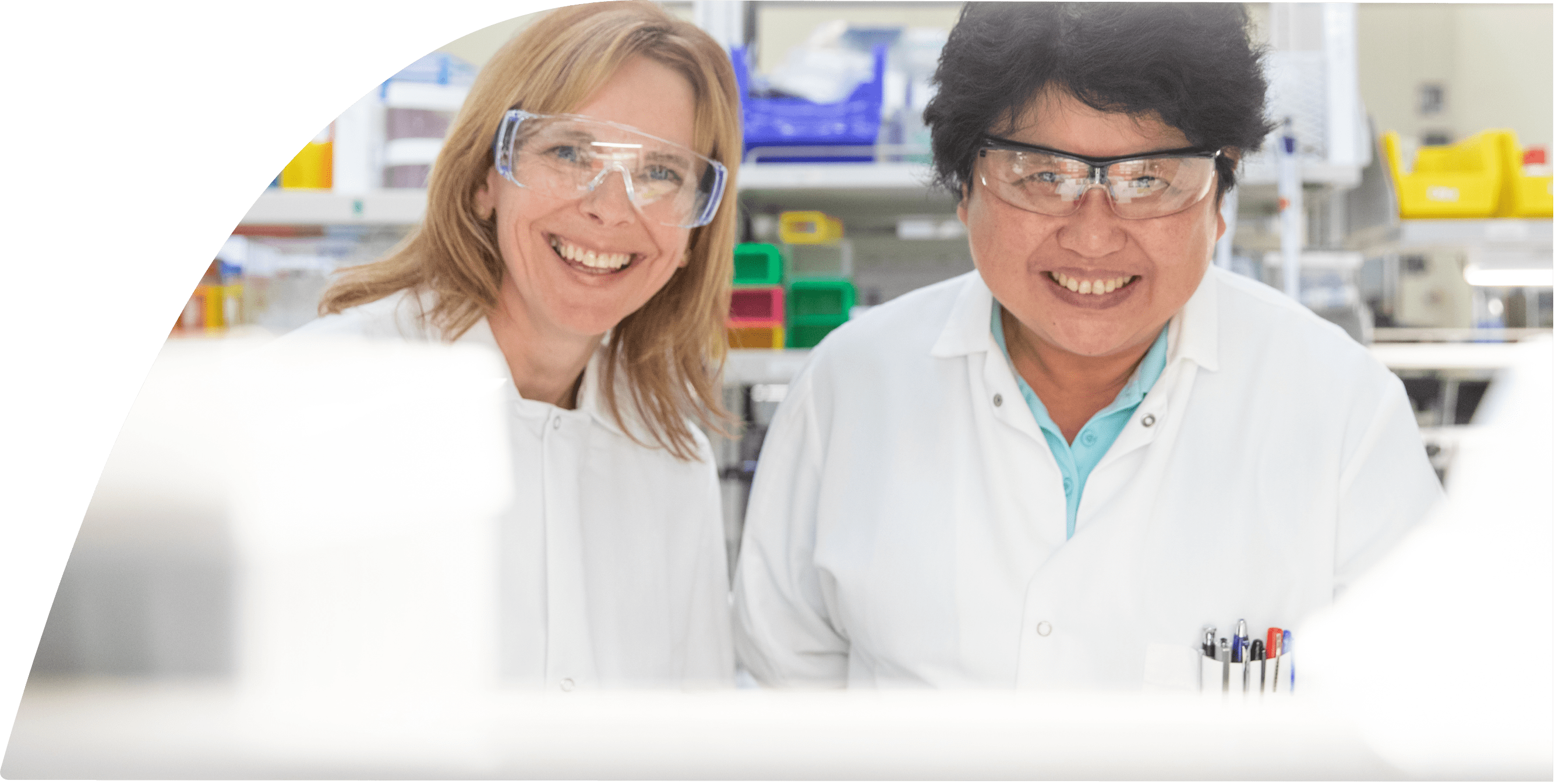
Engineer - Process & Equipment
Ireland - Dun Laoghaire Apply NowProcess & Equipment Engineer
Job Description
Amgen Dun Laoghaire (ADL) is looking for an Inspection & Packaging Engineer to join our Inspection & Packaging team to support the continued expansion of the plant and production capability on site. Amgen Dun Laoghaire (ADL) is a 37,000 square metre aseptic drug product operations facility, specialising in secondary manufacturing activities – Formulation, Vial/Syringe Filling, Lyophilisation and Packaging.
This position will be responsible for performance of packaging & inspection equipment on site. The engineer will report to the Engineering Manager and should have knowledge and proficiency in the use of statistical analysis tools, continuous improvement methodologies, problem solving and applied engineering skills relating to mechanical, electro-mechanical and associated automation systems. The engineer will also have full overall responsibility for the reliability and life cycle of equipment.
Key Responsibilities
- Support a safe working environment by complying with all pertinent environmental health/safety practice, rules and regulations.
- Ownership of equipment/systems in a GMP regulated manufacturing setting.
- Monitoring of day-to-day performance of their assigned system.
- Data trend analysis of all performance aspects of their system and equipment to identify and proactively manage performance trends.
- Proactively identify opportunities for improvement in equipment & processes as well as Preventative maintenance support to technicians for regular activities.
- Lead and support system improvements, development of detailed specifications, engineering documents and standard operating procedures.
- Lead technical root cause analysis, incident investigations and troubleshooting issues related to manufacturing equipment/systems.
- Working in a collaborative manner within the Process Teams structure and contributes to investigations, Non-Conformance and CAPA closure.
- Ensuring that a critical spare parts list for their system is identified and appropriate levels of spares are maintained.
- Maintain a structured plan for future improvements and downtime for equipment.
- Support new product introductions or new technology introductions by performing engineering assessments, implementation of system changes and supporting engineering runs.
Basic Qualification
- Bachelor degree in engineering (Mechanical, Electrical or Chemical preferred)
Preferred Qualification
- Manufacturing experience in medical device or pharmaceutical inspection or packaging.
- Solid leadership, technical writing, and communication/presentation skills
- Experience in change control, non-conformance, corrective and preventative actions, and validation practices
- Ability to influence the development of business area strategy and engineering/equipment strategy where appropriate
- Day to day vendor management and contract negotiations with focus on equipment suppliers
- Independent, self-motivated, organized, able to multi-task in a production environment
- Team player, prepared to work in and embrace a team-based culture that relies on collaboration, support other areas to meet business requirements.
Travel at various times may be required to support execution of projects